Wickliffe has made a decision to stay with tried and tested technology, purchasing a Ryobi 1050 press through Cyber New Zealand, and installing it into its Mt Wellington plant.
Dave Brown, production manager at Wickliffe, says, “We already had a Ryobi A1 press but we had no redundancy contingency for extra work at times like Christmas or for servicing requirements. We’ve always been very happy with the Ryobi presses, so it made sense to look at another Ryobi.”
The new press will serve several purposes at Wickliffe. He says, “We will use it partly for packaging and it will also help productivity on the 10 colour. Most of the work on the 10 colour is perfected work. This will save time and we envisage there will be real productivity gains.”
Wickliffe makes good use of its other two Ryobi presses in the Mt Wellington plant. He says, “We have plenty of work on. It is coming out of our ears at the moment. Having just one A1 press here in Auckland will no longer be an issue. Of course, we do have an A1 press in Christchurch but there’s freight to consider.”
“We already have a short run packaging capability and this new Ryobi press will complement that nicely. With short run jobs, we try to do the entire work in house but it depends on the run size and the delivery expectation.”
Dave Brown has 28 years’ experience at Wickliffe and he sees a bright future with the new Ryobi. He adds, “We are quite excited about this new press not just because of its timely arrival, especially in meeting our sales team’s expectations, but it will also give us more flexibility overall.”
The Ryobi 1050 press has a number of features that increase productivity for print companies. While models in the 1050 series come standard with the Ryobi semi-automatic plate changer, Wickliffe has opted for the fully automatic plate changer. Plate mounting and removal is entirely controlled from the press’s touch panel, leaving the press operator free to carry out other tasks while the plates are automatically changed. There is no need to bend the plates leading or tail edge.
The Ryobi 1050 at Wickliffe gives an option for the operator to enter pre-set values for paper size and thickness. The operator can also use the touch panel to pre-set the positions of the feeder head and delivery section guides.
The Ryobi programme inking automatically sets the conversion curve for each colour according to the image area ratio calculated at prepress. The ink settings, ink fountain roller speed, and the number of contacts by the ink doctor roller are controlled based on the conversion curves to assure the optimum ink volume. This function allows the operator to proceed to the next job. Ryobi says this also minimises paper wastage at the start of printing.
The press also provides various automatic cleaning devices to reduce the time and effort involved in cleaning and changing colours. The operator can turn each device on and off as well as selecting the cleaning pattern according to the required degree of cleaning.
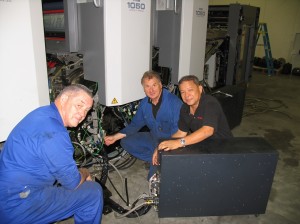
The Ryobi PQS, an in line printing quality control system, controls ink density during the print run. A CCD camera, mounted at the delivery section, takes a digital image to measure the density of the colour bar on the printed sheets. Values needed to correct the colour densities to match those of target densities are calculated and provided as feedback to the printing control system, which adjusts the opening of the ink fountain keys. Ryobi says this system can detect print defects like hickeys. It automatically marks out flawed printed sheets from non-defective sheets by inserting marker tapes.
The press uses a double diameter impression cylinder and a double diameter transfer drum. An optional moveable shell type skeleton transfer drum accommodates different print stock types and thicknesses by shifting the shell. Ryobi says it ensures consistent print quality by minimising scratching and marking of print stock.