Heidelberg has introduced a short inking technology for its Anicolor 2 system, aimed at delivering an optimum solution package for the flexible production of short runs.
Stephan Plenz, member of the management board responsible for Heidelberg equipment, says, “Our customers have their challenges, and we have the solutions and answers they need in the area of both digital and offset printing. The Anicolor technology is used in both small and medium production runs, and its scope of application will be increased once again with the new Anicolor 2.”
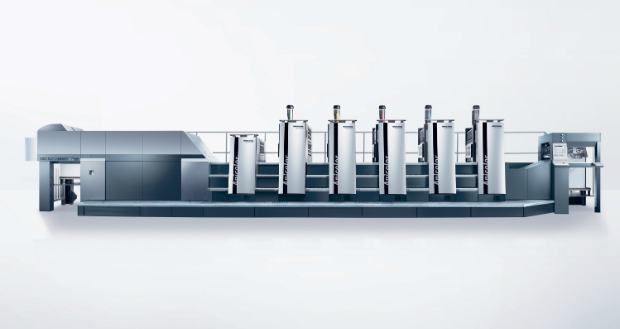
Heidelberg will demonstrate its Speedmaster XL 75 Anicolor 2 at drupa 2016
The company makes some bold statements around the new system, claiming around 90 percent less waste; 20 to 30 start-up sheets to reach the correct ink levels for a new order; and a 50 percent reduction in setup times combined with a 50 percent increase in productivity.
Heidelberg will demonstrate its next generation Anicolor technology at drupa 2016 with a Speedmaster XL 75 Anicolor 2. It says the new press system has three major innovations. The first, called Anicolor Booster, activated by pushing a button on the Prinect Press Centre, permits a wider range of inks thanks to an improved setting range for ink density on different printing stocks, according to Heidelberg, which adds that, in most cases, this does away with the need to change the ink chamber as was previously required with very absorbent printing stocks. The company says this shortens the setup time in commercial printing because operators can now process coated and uncoated paper with the same ink series. It claims a greater benefit in packaging printing, with the use of spot colours, up to 15 minutes saved here by not having to change the screen roller.
The second innovation involves a faster wash up programme that provides for faster ink changes and shorter set up times thanks to 9000 revolutions per hour instead of the previous 7000. The company claims operators can achieve changing colour shades up to a minute faster. This enables packaging printers facing two or more ink changes in almost every new order to get through two or three orders a day more.
The third innovations uses a function allowing the operator to choose between standard, short, or none for the ink shut-off time, depending on the colour assignment from one job to the next. Heidelberg says the shortened ink shut-off saves another 20 seconds, while eliminating it altogether reduces the setup time by 40 seconds.
Plenz says, “We presented the Speedmaster XL 75 Anicolor as prototypes at drupa 2012. We have sold over 200 printing units since then – split down the middle between commercial and packaging printers.
“At drupa 2016, we will show how easy it can be to complete short production runs quickly, flexibly, and economically using offset printing with the Speedmaster XL 75 Anicolor 2. Another aspect of this is machine and materials coming together in perfect harmony and enabling a standardised and fast overall process together with the Prinect workflow.”
Visitors to drupa can see the Speedmaster XL 75 Anicolor 2 at the IST stand in Hall 2. Heidelberg says the six-colour press with coating unit includes full UV functionality. Plenz adds, “We will show how material costs can be significantly reduced since Anicolor 2 enables UV applications to be processed on expensive, non-absorbent printing stock with very few makeready sheets.
“Anicolor 2 with a new design, new feeder, and the new Prinect Press Center XL 2 will be available as standard from November 2016. A number of technical functions such as the new Anicolor Booster and the faster wash up programmes will be available earlier from July 2016.”