The world’s oldest press maker says its enhanced Rapida 145 will feature as possibly the only high-tech large-format press running at drupa 2016.
KBA says it will equip the six-colour press with coater and automated pile logistics with a raft of new highlights aimed at automation. It will offer a higher maximum speed of 18,000sph and new double-pile delivery.
The new double-pile delivery has a waste-free delivery pile, which stands next to a smaller pile of waste, for sending straight to a die-cutter or laminating machine to be converted. KBA says this increases productivity because it eliminates the need to manually sort through a pile for waste.
It adds that operators can embed both piles in substrate logistics. With waste ejected at full speed of 18,000sph. It removes start-up and run-up waste automatically. KBA says you achieve production with two piles in manual and automatic mode.
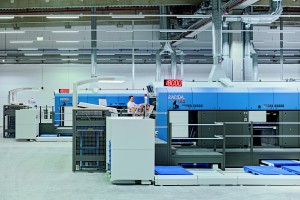
The KBA Rapida 145 will print 18000sph
Colour imposition, dampening, and the number of colours influence the substrate and that can lead to variations in print length. KBA says that stretching the printing plate along the axis and radius of the cylinder by up to 0.2mm on Rapida jumbos can compensate for the print length. It does not require manual intervention and results in improved print quality and less waste.
The company also claims advances in inline colour control. Green and red lights show the operator at the console’s monitor whether the colour densities fall within specified tolerances. A sound signals deviations and prompts immediate corrections.
For large format, KBA will unveil an inline sheet inspection as part of automatic quality control during printing. It compares a freshly printed sheet with the contents of a PDF file from prepress. After approving the reference sheet, production monitoring creates a virtual reference as soon as the OK sheet counter starts. A camera with a resolution of around 300dpi detects up to 90µm, even at maximum press speed. The inspection parameters can be adjusted during printing. The operator can find detailed information on possible sheet errors on the console’s wall screen. Certificates and reports provide detailed information on the print quality.
It also uses an additional tool, called QualiTronic PDF Pile View, for subsequent error analysis following production or in the case of complaints. KBA says the precise control of the entire job eliminates waste and prevents the customer from delivering faulty sheets.
The company says the new system boasts above-floor assembly and a low installation height. It does away with interfering with the hall floor or a building’s foundations. The piles are transported via LOX bands and servo motors. It uses a clear and simple user interface and plug and play components.
The pile turner has an individually controlled programme for preparing the pile. Operators can set vibration duration, air supply, pile position or mechanical strain on the substrate according to material. The system extracts the top three to five waste sheets automatically during pile preparation.
Operators can track press performance, the resulting energy consumption, and individual components, such as the dryer at the console in real time. The software logs and stores the energy consumed according to job. KBA has a solution called VisuEnergy solution for analysing all energy consumers in a printing house. These can then serve as input variables for a company’s energy management system.